Jak rozhartować stal?
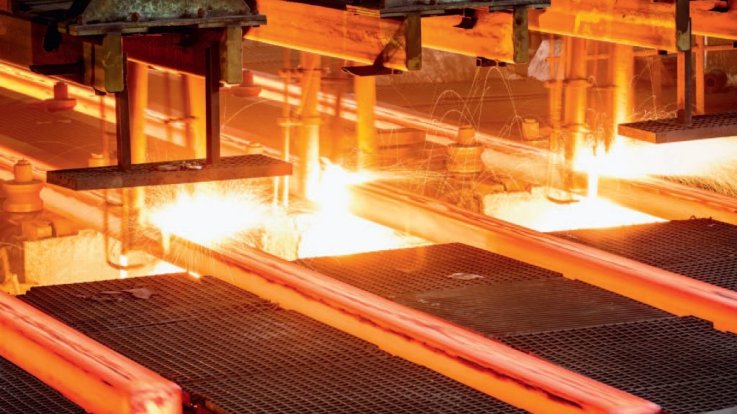
Stal, wytrzymały i wszechstronny materiał, jest fundamentem współczesnej metalurgii oraz przemysłu. Od jej struktury i właściwości zależy niezliczona ilość aplikacji, od narzędzi ręcznych po struktury inżynieryjne. Jednakże zdolność do modyfikowania i kontrolowania właściwości stali jest kluczowa dla wielu procesów produkcyjnych. Dlatego wiedza na temat jak rozhartować stal staje się niezastąpiona. Rozhartowanie, proces odwrotny do hartowania, ma na celu zmniejszenie twardości stali, przywracając jej plastyczność i wytrzymałość na pękanie. W niniejszym artykule prześledzimy krok po kroku, jak rozhartować stal, dowiemy się, dlaczego jest to niezbędne i jakie techniki są stosowane w tym procesie.
Co to jest rozhartowanie stali?
Rozhartowanie stali, zwane również odpuszczaniem, polega na zmniejszeniu twardości materiału, który wcześniej był poddawany hartowaniu. Hartowanie służy do zwiększenia twardości i wytrzymałości materiału, jednakże proces ten może uczynić stal kruchą i podatną na pękanie. Rozhartowanie natomiast odwraca część efektów hartowania, czyniąc stal bardziej elastyczną i odporną na pęknięcia. Proces ten jest niezbędny w przypadku niektórych zastosowań stali, takich jak produkcja narzędzi czy elementów konstrukcyjnych.
Stal rozgrzewa się w kontrolowany sposób i stopniowo schładza, aby osiągnąć pożądane właściwości. Czas i temperatura zależą od składu chemicznego stali oraz końcowego przeznaczenia materiału. Proces ten może być przeprowadzany na różne sposoby, w tym w piecach przemysłowych, przy użyciu palników gazowych lub za pomocą indukcji elektromagnetycznej.
Dlaczego rozhartowanie stali jest niezbędne?
Zapewnienie wytrzymałości mechanicznej
Głównym celem rozhartowania stali jest poprawienie jej wytrzymałości mechanicznej. Stal po przeprowadzeniu hartowania staje się bardzo twarda, ale również krucha, co z czasem może skutkować pęknięciami i uszkodzeniami. Rozhartowanie pozwala na uzyskanie materiału, który jest jednocześnie twardy i elastyczny. To oznacza, że stal nie tylko wytrzyma większe obciążenia, ale również lepiej zniesie warunki eksploatacyjne.
Redukcja naprężeń wewnętrznych
Hartowanie wprowadza do stali znaczne naprężenia wewnętrzne, które mogą prowadzić do jej deformacji lub nawet pękania w trakcie użytkowania. Rozhartowanie działa jak swoisty "spokój" dla materiału, redukując te napięcia i zapewniając stabilność strukturalną. To jest kluczowe w przypadku części maszyn, gdzie precyzja i stabilność są niezbędne.
Poprawa struktury mikroskopowej
Kolejnym ważnym aspektem jest korekta struktury mikroskopowej stali. Proces hartowania, mimo że dodaje twardości, może prowadzić do tworzenia się niepożądanych faz, takich jak martenzyt, który jest bardzo kruchy. Rozhartowanie przekształca martenzyt w bainit lub ferryt, które są bardziej stabilne i odporne na pękanie. Dzięki temu stal zyskuje optymalną kombinację twardości i elastyczności.
Zwiększenie odporności na korozję
Podczas hartowania, stal może wchodzić w reakcje z tlenem, co prowadzi do utlenienia powierzchni. Rozhartowanie zmniejsza ryzyko wystąpienia korozji poprzez stabilizację struktury materiału. Dzięki temu stal zachowuje swoje właściwości estetyczne i funkcjonalne przez dłuższy czas, co jest szczególnie ważne w przypadku elementów narażonych na działanie czynników atmosferycznych.
Umożliwienie dalszej obróbki
Często stal po hartowaniu jest zbyt twarda, aby poddać ją dalszej obróbce, takiej jak frezowanie, toczenie czy wiercenie. Rozhartowanie umożliwia przeprowadzenie tych procesów w sposób bezpieczny i efektywny, przy mniejszym ryzyku uszkodzenia narzędzi czy samego materiału.
Techniki rozhartowania stali
Odpuszczanie w piecu
Odpuszczanie w piecu jest jedną z najbardziej powszechnych technik rozhartowania stali. Proces ten polega na umieszczeniu stali w piecu i stopniowym podgrzewaniu jej do wymaganej temperatury, która zależy od składu chemicznego stali oraz pożądanych właściwości końcowych. Temperatura ta zazwyczaj wynosi od 150°C do 700°C, choć dla niektórych specjalistycznych stali może być wyższa.
Po osiągnięciu pożądanej temperatury, stal jest utrzymywana w piecu przez określony czas, zazwyczaj od kilkudziesięciu minut do kilku godzin. Czas ten pozwala na pełne ustabilizowanie struktury materiału i redukcję naprężeń wewnętrznych. Po zakończeniu procesu ogrzewania, stal jest stopniowo schładzana, co jest kluczowym etapem, ponieważ zbyt szybkie schładzanie może prowadzić do powtórnego wprowadzenia naprężeń.
Wykorzystanie palników gazowych
Palniki gazowe oferują szybki i efektywny sposób na rozmęczenie małych lub średnich elementów stalowych, szczególnie w warunkach warsztatowych. Ten proces polega na miejscowym podgrzewaniu stali do odpowiedniej temperatury z wykorzystaniem palników na propan-butan lub acetylenu.
Główne zalety wykorzystania palników gazowych to precyzyjna kontrola nad procesem oraz możliwość rozegrzewania wybranych sekcji materiału, bez konieczności podgrzewania całego obiektu. Wadą tej metody może być trudność w utrzymaniu stabilnej i równomiernej temperatury na całej powierzchni materiału, co może skutkować niejednorodnym rozmęczeniem.
Aby uzyskać optymalne rezultaty, warto skorzystać z osłon gazowych, takich jak argon czy azot, które minimalizują ryzyko utlenienia oraz kontaminacji powierzchni stali podczas procesu podgrzewania.
Rozhartowanie przy użyciu indukcji
Indukcja elektromagnetyczna to innowacyjna technologia pozwalająca na szybkie i precyzyjne rozhartowanie stali. Proces ten wykorzystuje prądy wirowe generowane przez pole elektromagnetyczne, które nagrzewają stal do wymaganej temperatury. Po osiągnięciu pożądanej temperatury, materiał jest stopniowo schładzany, podobnie jak w innych metodach rozhartowania.
Technologia ta oferuje liczne korzyści, w tym szybsze nagrzewanie, większą precyzję oraz mniejsze zużycie energii. Dodatkowo, dzięki swojej precyzji, metoda ta jest często wykorzystywana do rozkładania specyficznych sekcji lub komponentów stalowych, gdzie wymagana jest wysoka dokładność termiczna.
Metoda solnych kąpieli
Kąpiel solna to metoda polegająca na zanurzeniu stali w roztworze soli o wysokiej temperaturze, zwykle składającym się z azotanu sodu (NaNO3) i azotanu potasu (KNO3). Roztwór ten jest podgrzewany do temperatury w zakresie od 150°C do 700°C w zależności od wymagań materiału.
Zaletą tej metody jest równomierne i szybkie nagrzewanie stalowych komponentów, co pozwala na uzyskanie jednorodnych warunków rozmęczania. Wadą może być konieczność stosowania specjalistycznego sprzętu oraz ryzyko korozji, jeśli proces nie jest przeprowadzany w odpowiednich warunkach.
Wygrzewanie w piecu komorowym
Piecy komorowe, popularne w dużych zakładach przemysłowych, oferują możliwość rozmęczania dużych partii stali jednocześnie. Proces ten polega na umieszczeniu materiałów w komorze pieca, która jest szczelnie zamknięta i podgrzewana do wymaganej temperatury.
Główne zalety tej metody to możliwość kontroli atmosfery wewnątrz komory (np. poprzez wprowadzenie gazu obojętnego), efektywność energetyczna oraz zdolność do jednoczesnego przetwarzania dużych ilości materiału. Piec komorowy pozwala również na precyzyjne sterowanie zarówno temperaturą, jak i czasem trwania procesu, co gwarantuje wysoką jakość i powtarzalność wyników.
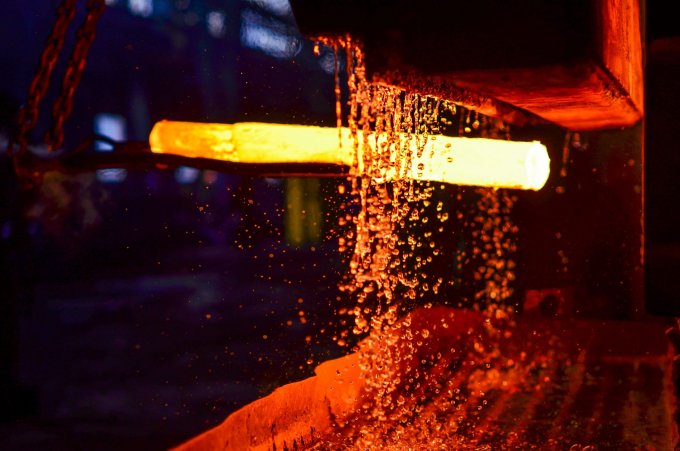
Jak przygotować stal do rozhartowania?
Wybór odpowiedniego materiału
Przygotowanie stali do procesu rozhartowania wymaga pełnego zrozumienia właściwości materiału. Różne gatunki stali wymagają różnorodnych podejść. Należy dokonać właściwego wyboru na podstawie składu chemicznego i wcześniejszych procesów obróbki. Często stosowanymi gatunkami są stale węglowe, chromowo-niklowe, czy narzędziowe, które mają różne właściwości i wymagania temperaturowe.
Na etykiecie lub certyfikacie materiału powinny być zawarte informacje dotyczące składu chemicznego, co pozwala na właściwe ustawienie parametrów rozhartowania. Unikanie materiałów o nieznanym składzie chemicznym jest kluczowe dla uzyskania przewidywalnych rezultatów.
Czyszczenie i odtłuszczanie powierzchni
Przed przeprowadzeniem procesu rozhartowania niezbędne jest dokładne oczyszczenie i odtłuszczenie powierzchni stali. Pozostałości olejów, smarów, rdzy czy innych zanieczyszczeń mogą wpłynąć na jakość rozmęczania i prowadzić do niejednorodnych właściwości końcowych.
W celu czyszczenia można użyć różnych metod, takich jak kąpiele chemiczne, piaskowanie czy ultradźwięki. Odtłuszczanie natomiast najczęściej przeprowadza się za pomocą rozpuszczalników organicznych, takich jak aceton, czy za pomocą specjalistycznych myjek przemysłowych.
Kontrola wymiarów i geometrii
Podczas procesów cieplnych stalowych komponentów dochodzi do zmian wymiarowych. Przed rozhartowaniem warto zatem dokładnie zmierzyć wszystkie kluczowe wymiary, aby móc je kontrolować i kompensować ewentualne zmiany po zakończeniu procesu. W przypadku precyzyjnych elementów, takich jak części maszyn czy narzędzia, dokładność wymiarów ma kluczowe znaczenie.
Wyposażenie warsztatu w odpowiednie narzędzia pomiarowe, takie jak mikrometry, suwmiarki czy czujniki zegarowe, pozwala na precyzyjne określenie wymiarów przed i po procesie rozhartowania.
Przygotowanie środowiska
Aby proces rozhartowania przebiegł zgodnie z planem, należy również zadbać o odpowiednie przygotowanie środowiska pracy. Upewnij się, że wszystkie narzędzia i urządzenia są w pełni sprawne i skalibrowane. Warto także zwrócić uwagę na właściwą wentylację przestrzeni roboczej, szczególnie jeśli używasz palników gazowych lub pracujesz z substancjami chemicznymi.
Kontrola bezpieczeństwa to także kluczowy aspekt. Wszelkie procesy termiczne wiążą się z ryzykiem wypadków, dlatego niezbędne jest stosowanie odpowiednich środków ochrony osobistej, takich jak rękawice, okulary ochronne i odzież ognioodporną.
Ustalanie parametrów procesowych
Na koniec, przed rozpoczęciem procesu rozhartowania, ważne jest ustalenie wszystkich parametrów procesowych na podstawie gatunku stali i jej zamierzonego zastosowania. Na przykład, dla stali węglowej proces rozhartowania może wymagać temperatury w przedziale 150°C do 250°C, podczas gdy stale narzędziowe mogą wymagać wyższych temperatur.
Nieoceniona może okazać się konsultacja z podręcznikami metalurgicznymi, tabelami temperatur dla różnych gatunków stali oraz specjalistami pracującymi w tej dziedzinie.
Potencjalne błędy i jak ich unikać?
Niedostateczne oczyszczenie powierzchni
Jednym z najczęstszych błędów jest niedostateczne oczyszczenie powierzchni przed rozpoczęciem procesu rozhartowania. Zanieczyszczenia mogą wpłynąć na nierównomierne nagrzewanie oraz wprowadzić defekty do struktury materiału. Aby tego uniknąć, zawsze upewnij się, że powierzchnia stali jest wolna od olejów, smarów czy rdzy. Regularne stosowanie środków chemicznych do czyszczenia oraz kontrolowanie procesu odtłuszczania są kluczowe.
Zbyt szybkie schładzanie
Kolejnym częstym błędem jest zbyt szybkie schładzanie po zakończeniu procesu nagrzewania. Szybkie schładzanie może prowadzić do powtórnego zahartowania części stali, co niweczy efekt końcowy. Aby uniknąć tego problemu, schładzaj stal powoli i w kontrolowany sposób. Można to zrobić na przykład przez stopniowe obniżanie temperatury pieca lub zastosowanie kąpieli wodnej o kontrolowanej temperaturze.
Nieodpowiednia kontrola temperatury
Równomierne i precyzyjne nagrzewanie jest kluczowe dla uzyskania optymalnych wyników. Niewłaściwa kontrola temperatury może prowadzić do lokalnych przegrzewań lub niepełnego rozhartowania. Wykorzystywanie nowoczesnych termopar i systemów kontrolujących temperaturę może zredukować ryzyko błędów. Regularne kalibracje urządzeń pomiarowych także mają swoje znaczenie w zapewnieniu wysokiej jakości procesu.
Ignorowanie specyfikacji materiału
Każdy rodzaj stali ma swoje unikalne wymagania i specyfikacje dotyczące temperatur i czasu trwania procesu rozhartowania. Ignorowanie tych specyfikacji może prowadzić do uzyskania materiału o niewłaściwych właściwościach mechanicznych. Zawsze sprawdzaj certyfikaty i dokumentację techniczną materiału przed rozpoczęciem procesu oraz konsultuj się z fachowym literaturą i ekspertami w dziedzinie metalurgii.
Nieodpowiednie narzędzia i sprzęt
Korzystanie z niewłaściwych narzędzi i urządzeń to kolejny potencjalny problem. Piecy, palniki, czy nawet kąpiele solne muszą być odpowiednio dostosowane do rodzaju i rozmiaru obrabianego materiału. Nawet najdrobniejsze narzędzie pomiarowe, jak nieodpowiednio skalibrowany termometr, może wprowadzić znaczące błędy do procesu. Regularna konserwacja i kalibracja sprzętu są niezmiernie istotne.
Brak odpowiedniej wentylacji i środków bezpieczeństwa
Zapewnienie odpowiedniej wentylacji oraz stosowanie środków ochrony osobistej to także aspekty, których zaniedbanie może prowadzić do poważnych problemów. Metalurgiczne procesy termiczne wiążą się z wytwarzaniem szkodliwych gazów i pyłów. Stosowanie masek ochronnych, odzieży ognioodpornej i odpowiedniego systemu wentylacyjnego jest nie tylko zalecane, ale wręcz konieczne.
Wskazówki od ekspertów
Dr inż. Jan Kowalski, specjalista ds. metalurgii
"Proces rozhartowania stali jest niezwykle wymagający i precyzyjny. Ważne jest, aby pamiętać, że każda zmiana w parametrach procesu, nawet najmniejsza, może mieć znaczący wpływ na końcowe właściwości stali. Dlatego zalecam, aby zawsze pracować zgodnie ze specyfikacjami materiałowymi i konsultować każdy krok z profesjonalistami."
Monika Nowak, inżynier materiałowy
"Nie należy lekceważyć znaczenia właściwego przygotowania powierzchni do rozmęczania. Nawet najmniejsze zanieczyszczenie może wpłynąć na jakość końcowego produktu. Również równomierne podgrzewanie jest kluczowe, dlatego zainwestowanie w dobrej jakości piec lub palnik to podstawa."
Andrzej Wiśniewski, technolog przemysłowy
"Unikanie błędów to połowa sukcesu. W mojej praktyce najczęściej spotykaną przyczyną problemów jest zbyt szybkie schładzanie oraz niedostateczna kontrola temperatury. Korzystanie z nowoczesnych urządzeń pomiarowych i systemów kontroli procesów jest nieocenione. Nigdy nie oszczędzaj na jakości sprzętu."
Podsumowanie
Stal jest fundamentalnym materiałem w metalurgii i przemyśle, cenionym za swoją wytrzymałość i wszechstronność. Proces rozhartowania, czyli zmniejszenia twardości stali, jest niezbędny, aby przywrócić jej plastyczność i wytrzymałość na pękanie. Dzięki temu stal staje się bardziej elastyczna i odporna na pęknięcia, co jest kluczowe w produkcji narzędzi i elementów konstrukcyjnych. Rozhartowanie redukuje naprężenia wewnętrzne, poprawia strukturę mikroskopową, zwiększa odporność na korozję i umożliwia dalszą obróbkę materiału. Proces ten może być przeprowadzany różnymi metodami, w tym w piecach, przy użyciu palników gazowych, indukcji elektromagnetycznej czy kąpieli solnych. Ważne jest odpowiednie przygotowanie stali, w tym oczyszczenie powierzchni i kontrola wymiarów, aby osiągnąć optymalne rezultaty i uniknąć potencjalnych błędów.